Dane zbierane w czasie rzeczywistym na potrzeby optymalizacji procesów
Praktyczne oprogramowanie do obróbki mechanicznej
Firma Walter – specjalizująca się w obróbce mechanicznej – już kilka lat temu postanowiła się zmierzyć z kwestią cyfryzacji. W ramach linii Walter Nexxt oferuje produkty cyfrowe i rozwiązania zgodne z koncepcją Przemysłu 4.0, dostosowane do potrzeb średnich przedsiębiorstw. Jednak Walter zajmuje się procesem produkcyjnym i jego planowaniem na różnych poziomach. Dobrymi przykładami są tu oprogramowanie Comara iCut do optymalizacji danych dotyczących skrawania i platforma Comara appCom do monitorowania procesów produkcyjnych.
Cyfryzacja, produkcja sieciowa, duże zbiory danych, Internet Rzeczy (IoT) – te tematy są wszechobecne. Dlaczego więc hasło „Przemysł 4.0” budzi niepokój wśród pracowników technicznych w wielu firmach średniej wielkości? Dzieje się tak, ponieważ nie są pewni, co oznacza ten termin w ich codziennej pracy, w strategii produkcji nastawionej na przyszłość i w planowaniu.
Adaptacyjna regulacja posuwu: optymalizacja skrawania na podstawie danych uzyskiwanych w czasie rzeczywistym
Automatyzacja, cyfryzacja i procesy sieciowe to już codzienność w wielu dziedzinach produkcji przemysłowej. Dalszą optymalizację procesów udaje się uzyskać dzięki zwiększaniu wydajności sprzętu i oprogramowania do zbierania i analizowania danych w czasie rzeczywistym. Przykładowo: działanie oprogramowania Comara iCut firmy Walter opiera się na analizie danych z maszyn przychodzących w czasie rzeczywistym.
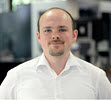
Oprogramowanie iCut integruje się z programem sterującym i korzysta z danych do realizacji procesu obróbki mechanicznej. Przy pierwszym cięciu iCut „uczy się” mocy biegu jałowego wrzeciona i maksymalnej wydajności skrawania na jedno cięcie. Następnie mierzy moc wrzeciona do 500 razy na sekundę i automatycznie dostosowuje posuw. W rezultacie, gdy tylko jest to możliwe, maszyna pracuje z maksymalnym posuwem, którego „nauczyło się” oprogramowanie iCut dla każdego narzędzia. Jeśli warunki skrawania ulegną zmianie, np. ze względu na różne kąty frezowania i głębokości skrawania, wahania tolerancji albo oznaki zużycia narzędzia, oprogramowanie automatycznie dostosowuje prędkość i wydajność w czasie rzeczywistym.
Te pozytywne skutki nie ograniczają się do czasu obróbki elementów, a niezawodność procesu zwiększają również zoptymalizowane parametry frezowania. Siły działające na wrzeciono charakteryzują się większą stałością, co wydłuża żywotność wrzeciona. Jeżeli narzędziu grozi uszkodzenie, oprogramowanie iCut natychmiast zmniejsza posuw lub wstrzymuje pracę.
Z oprogramowania iCut firmy Walter można korzystać nawet bez narzędzi Walter – wszystko, czego potrzeba, to spełnienie wymogów systemowych maszyny.
Większa niezawodność i wydajność procesu dzięki przejrzystym danym z maszyny
Specjaliści od oprogramowania w firmie Comara przystosowali oprogramowanie iCut do optymalizacji nawet specyficznych, wąsko zdefiniowanych procesów i stworzyli platformę appCom w celu wykorzystania wszystkich danych generowanych przez maszynę podczas obróbki w ramach optymalizacji procesów. Całe rozwiązanie jest tak proste i przejrzyste, jak to tylko możliwe.
Comara iCut dynamicznie dostosowuje posuw do warunków cięcia. Pozwala to skrócić czas obróbki elementu i zwiększyć niezawodność procesu (fot. Walter AG)
Rozwiązanie appCom firmy Comara składa się z komputera PC instalowanego w maszynach i zintegrowanego z systemem sterowania oraz oprogramowania analizującego i wyświetlającego dane. Nawet podstawowa wersja oprogramowania appCom zawiera ponad 13 aplikacji, z których można korzystać do zbierania i monitorowania najważniejszych parametrów optymalizacji procesów. Obejmują one status monitorowanych maszyn, ich wydajność, zadania i stabilność środowiska uruchomionych programów. Ważne parametry, raporty i dane pochodzące z monitorowania tak się przetwarza, aby były prezentowane w sposób zrozumiały.
Indywidualne przydzielanie praw dostępu
Indywidualnie przyznawane prawa określają, kto może wyświetlać dane. Operatorzy maszyny widzą tylko to, co jest im potrzebne. Natomiast menedżerowie odpowiedzialni za produkcję i planowanie mogą korzystać ze wszystkich opcji monitorowania.
Oprócz standardowych aplikacji na platformie appCom można utworzyć i wyświetlić aplikacje dla danej firmy. Aplikacje są widoczne w interfejsie internetowym dostępnym zarówno ze stacjonarnego komputera PC, jak i ze wszystkich popularnych urządzeń mobilnych. Z platformy appCom można korzystać, by zidentyfikować bieżące problemy i krytyczne procesy, a także by analizować procesy realizowane przez maszynę. Parametry obejmują wydajność, koszt pojedynczego narzędzia lub obrabianego elementu i niezawodność procesu. Dzięki temu można korzystać z danych uzyskiwanych w czasie rzeczywistym do optymalizacji i planowania produkcji bez konieczności ręcznego zestawiania informacji pochodzących z różnych programów monitorujących, przekazanych w różnych formatach.
Comara appCom – wszystkie istotne dane są przejrzyście ułożone, można je analizować i wyświetlać według różnych kryteriów (fot. Walter AG)
Platformę appCom można również podłączyć do systemów ERP. Aplikacja przetwarza pobrane dane i łączy je z danymi pochodzącymi z maszyny. Kolejną zaletą platformy appCom jest to, że nie korzysta z chmury. Kluczowe dla firmy dane znajdują się w komputerze z systemem appCom oraz na własnych serwerach firmy i nie są przechowywane w chmurze ani przez firmę Walter, ani przez żadnego innego dostawcę.
Potencjał oferowany przez narzędzia do monitorowania i analizy, takie jak oprogramowanie appCom, jest oczywisty dla firm zajmujących się obróbką skrawaniem, które zazwyczaj działają pod presją optymalizacji kosztów i wydajności. Trudno jest jednak ująć ten temat w konkretnych liczbach.
Różne czynniki mają wpływ na potencjalną efektywność i oszczędności płynące z wykorzystania takiej platformy jak appCom. Ważny jest stopień automatyzacji i cyfryzacji procesów produkcyjnych oraz to, jak istotna jest dla danego problemu operacja obróbki skrawaniem. Przykładowe dane są wprawdzie niejednoznaczne, ale klienci korzystający z appCom z całą pewnością dostrzegają znaczny wzrost produktywności i niezawodności procesu w odniesieniu do poszczególnych maszyn – podsumowuje Florian Böpple.
Źródło: Walter Polska